Embodied energy can be helpful when considering which products to use in construction for specific applications. Embodied energy is the energy used in every phase of production, transportation, and assembly of a given product. Determining the actual embodied energy of a specific product requires vast amounts of data and an in-depth knowledge of production practices. What we can do, though, is examine the distance a product travels during its production processes.
In this article, we will examine one of the centerpieces of WaterShed: the solar panel array, the energy plant of the house. WaterShed uses SANYO’s HIT 220A model solar panels. They are some of the most efficient panels consumers can purchase on the market today. The materials in the solar panels travel great distances during the production and assembly periods. But does the production transportation distances negate the positives provided from installing solar panels? We’ll take a look.
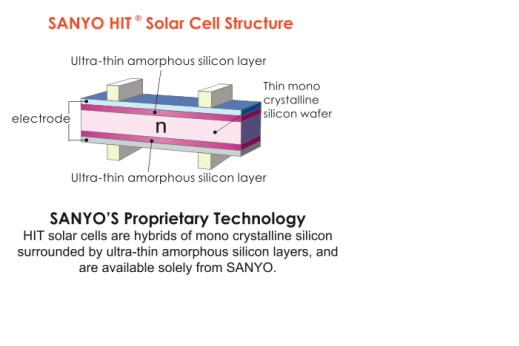
SANYO HIT Power® solar modules
Image Credit: SANYO
The Module:
SANYO HIT Power® solar modules are made of 72 hybrid HIT cells combining two best-of-breed solar technologies: high efficiency monocrystalline silicon with ultra-thin layers of amorphous silicon. The monocrystalline Si is sandwiched between the amorphous Si to offer superior conversion efficiency, excellent temperature characteristics and considerable output under diffuse and low light conditions. The HIT Power 220A module features certified cell efficiency of 19.8% and module efficiency of 17.4%, among the best the industry has to offer.
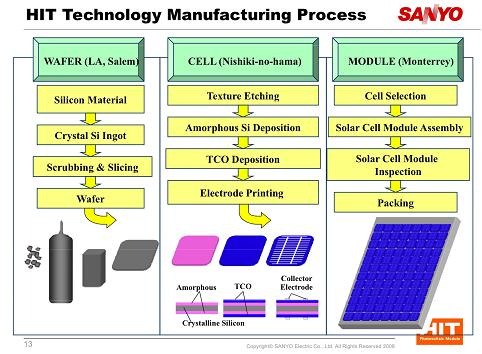
Sanyo HIT Technology Manufacturing Process
Image Credit: Sanyo
Production Process:
SANYO manufactures its own silicon ingots and wafers, core materials in the manufacturing of all SANYO solar cells and modules for North America, at SANYO facilities in Carson, CA and Salem, OR. Combined, the two plants have 100 MW wafer production capacity. These ingots and wafers are then shipped to facilities in Japan, where HIT technology is used to create the solar cells that will be the major component in all modules. There are two factories, the Nishikinohama Factory in Kaizuka City, Osaka Prefecture and the Shimane factory in Unnan City, Shimane Prefecture. They have a combined production capacity total of 340 MW the goal of reaching around 600 MW by the end of FY2010 for HIT solar cell production capacity. After the solar cells are produced they are shipped to Monterrey, Mexico for assembly in the final solar panel. The Monterray factory is capable of producing 50 MW annually. Other module assembly plants are located in Japan and Hungary, serving Asia and Europe respectively. SANYO also operates its North American Solar Sales office out of San Jose, CA.
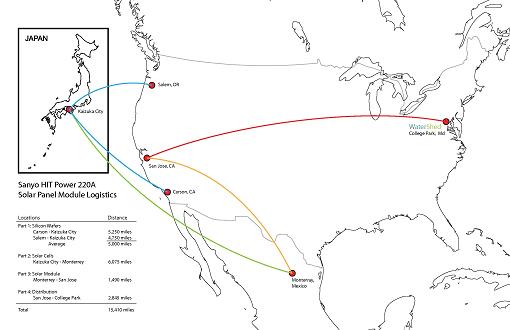
Solar Panel Module Logistics
Image Credit: Joseph Ijjas
Payoff:
HIT panels are 26% lighter per installed watt than the average solar panel with reduced package materials for lighter, cheaper, and more efficient storage and transportation. Even with one of the most efficient panels on the market, the question becomes whether the embodied energy in transportation and production negates the positives of benefits of installing solar panels? Simply put, no. If your panels were the only ones assembled and shipped through this process then it would be a great waste of resources and energy due to the distances traveled. But SANYO is approaching its goal of producing 600 MW annually. So when you consider a 10 kW system is capable of providing all the energy necessary in operating WaterShed, then it becomes a very simple decision. The benefits of using SANYO’s HIT panels for the production of clean, renewable energy are far greater than the resources and energy used in the production and transportation of panels and the use of standard energy sources on our local electrical grid. And if you were to add the benefits of every 10 kW system installed, the resources embodied in the production and transportation of the 220A panels becomes even more minimal. The takeaway then is the benefits outweigh the potential negatives.